UV Stability
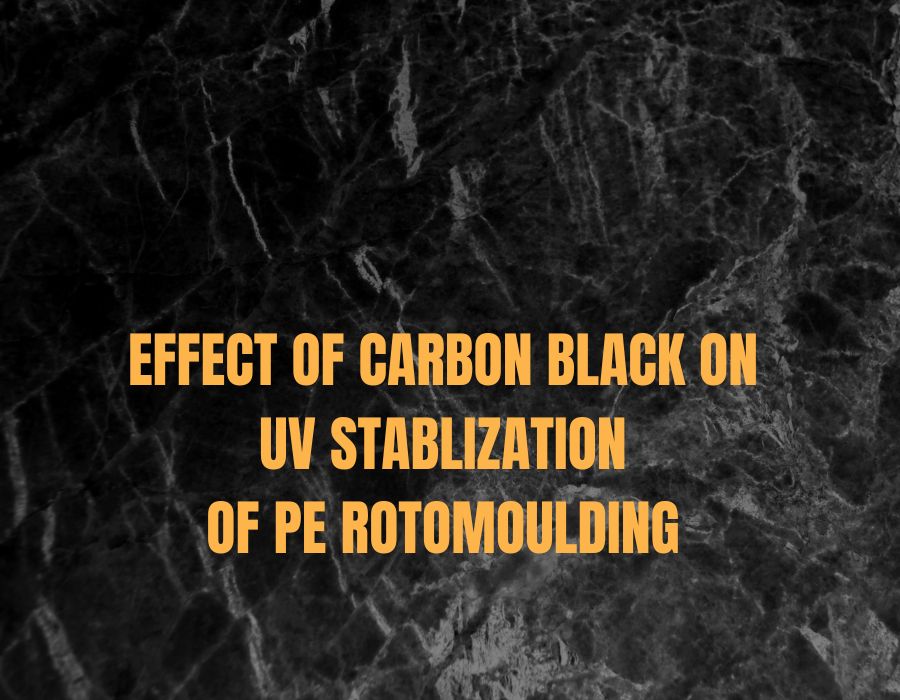
Effect of Carbon Black On UV Stabilization of PE Rotomoulding
Introduction of UV Stabilization’s:
Finished PE products designed for external applications may degrade in use, with time. They are said to “weather” when their structure changes due to light, heat, moisture and oxygen contact. Plastics absorb sunlight radiations and undergo photo-chemical reactions. Oxidation occurs leading to an alteration of their colour, texture or composition resulting in impact loss, embrittlement, chalking or surface cracking. Out of the whole solar emission spectrum, only the smallest part, the 290-400 nm UV region, is responsible for most of the polymer damage. Photo-oxidation of polyethylene proceeds by a free radical chain mechanism in presence of oxygen: the ultraviolet light absorbed by the polyethylene provides sufficient energy to break key molecular bonds and generate free radicals that propagate to give hydroperoxides, compounds containing hydroxyl, carbonyl and vinyl groups, which also absorb UV radiation and undergo further degradative processes. As a result, succession of chain scissions and chain recombination’s (crosslinking), including more fragile units, induces drastic physical degradations.
In order to limit or postpone the onset of degradation, several types of UV light stabilizers can be added to the polymer. The most important stabilizer types work by screening out the harmful ultraviolet light – for instance UV absorbers such as benzophenones or small dispersed particles such as carbon black or inorganic pigments. Other very effective UV stabilizers are UV quenchers and HALS (Hindered Amine Light Stabilizers).
UV Stability in Water Tanks:
Cylindrical vertical tanks are commonly used for outdoor applications and hence, usually manufactured from
polyethylene resin with addition of carbon black OR Colored with UV stabilizers.
Rotational moulded polyethylene water storage tanks may be produced either with monolayer or multilayer wall construction. For multilayer wall construction, the wall shall consist of minimum two layers to maximum five layers. Tanks produced from multilayer walls, provide improved overall performance and service life owing to each layer providing desired specific functional property. Each layer of the wall shall have uniform thickness.
For monolayer wall construction, compounded resin of polyethylene and carbon black shall be used. Carbon black provide desired outdoor weathering resistance. A fine, well-dispersed carbon black provides the best. For multilayer wall construction, the typical wall design comprises of inner layer, in contact with water, of white colour and the outer most layer, which is also exposed to the sunlight, shall be of black colour. The thickness of outer layer shall be minimum 50 percent of the total wall thickness. The middle layers, also called as core layers, may be a single layer for 3-layer tank to maximum three core layers for 5-layer tank. Core layers may be made of solid or foamed polyethylene.