Changes the face of Indian Rotomolding Industry
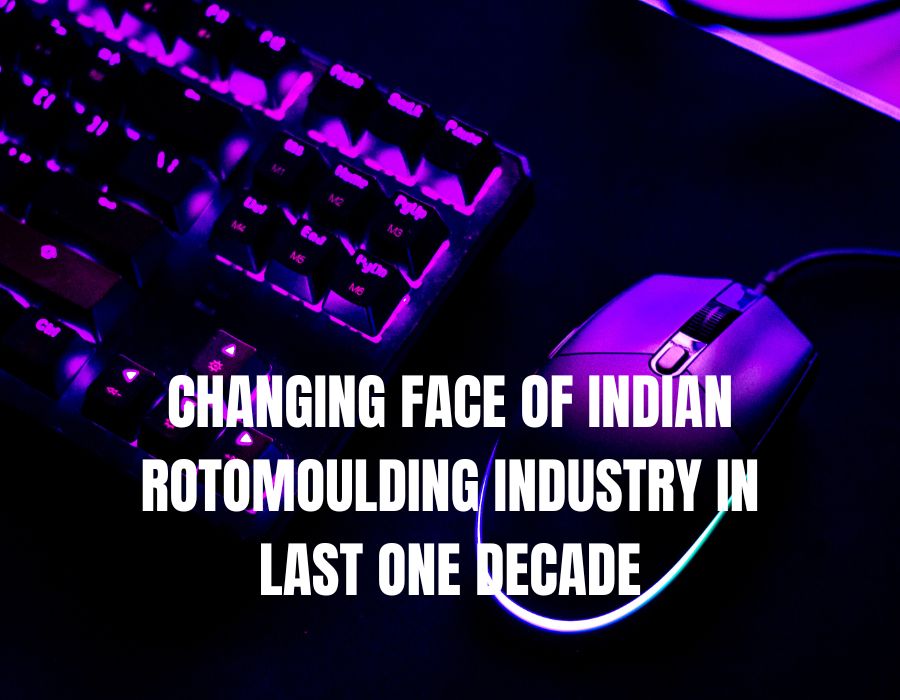
Changes the face of Indian Rotomolding industry in last one decade
‘Rotomolding’ is a wonderful process where industry always attracting due to higher profit margin, design freedom (complex designs possible), seamless products (no weld line), Several layers with uniform wall-thickness, Stress-free, insert moulding is key to win. Rotomoulding business is suitable for small size orders due to slow production cycle.
Rotomolding sector is always promising and made-for-passionate entrepreneurs. Indian economy is booming very fast & we have witnessed many revolutions like Digital revolutions (latest), Farm-to-Retail revolutions, green revolutions, Milk revolutions, Industrialization. India has large numbers of skilled younger manpower that is added advantage for growth of Indian economy. In last decade Retail sector, Infrastructure sector, Life style sector, Road safety sector, Material handling sector and Automotive sector grown in rapid pace. To cope-up growth of these sector there are huge demand of Rotomolded Product’s in India.
Many rotomolders witnessed multiple growth in Custom moulding sector and their turnover / profit increased multiple times. They added high output better technology efficient machines, developed quality products, developed skilled manpower added multiple processing units.
Indian Rotomolding sector witnessed a huge shifting from Tank sector to non-tank sector in last decade. In 2009 the ratio of Tanks: Non-tank was 90:10 and now it shifted to 70:30. The shifting takes place because High margins in Non-Tank (Custom moulding) products also many key attributes like org anise customers, secure payments from end-users, Less competition. Value-added non-tank (custom moulding) products needs attributes like commitment to Quality, Best service, On Time delivery and Total system production (Total solution).
Indian Rotomoulding market witnessed few better margin products like Road barriers for NHAI/Airports/Metro, Waste bins for Municipal corporations/ ‘Swachh Bharat Abhiyan’, School furniture’s for ‘Sarva Shiksha Abhiyan’, Manholes for Sewerage treatment, Fuel tanks for commercial vehicles like Ashok Leyland, TATA, Eicher, TAFE, New Holland, John Deere, Volvo, New Holland, JCB, etc.
Material notes: In material front Custom moulding products needs high performance in comparison of Tanks. To address their needs now many varieties of Rotomoulding materials are available in Indian market like Traditional LLDPE grades (in Butene, Hexene and Octene comonomer), 3rd generation Metallocene LLDPE grades, XLPE, pre-coloured powders, etc. Now Indian rotomolders have variety of resin suitable for applications. Better resin selection gives value additions to product like better ECSR, Tensile, Stiffness, Impact properties. Additives industry also given moral boost-up to Roto sector by better quality of Carbon black masterbatch, UV stabilizers, Anti-Oxidants, Antistats, etc. For underground applications high density LL grades, for Auto fuel tanks XLPE / Metallocene grades, for toys pre-coloured UV stabilised LL powders are most popular in India.
Butene is preferred choice for water tanks up to 10,000 Ltrs. Hexene and Octene are going popular for tanks ranges from 10KL to 25KL for better mechanical properties and thin-gauging. Hexene/Octene/XLPE/PP are the preferred choices for Chemical tanks and Diesel storage tanks. Addition of extra AO’s (Secondary and Primary) for large size tanks to take care thermal and photo degradation. UV stability is again challenging point with end-user’s asking from UV4 to UV20 depend on use of the tanks. Faster densification (faster bubble removal) is need of the hour for better productivity and quality. Pre-coloured ready-to-use powder is going popular for better results. Use of Expanded Polyethylene foam (EPE) in middle layer of tanks for heat insulations and higher rigidity. Size of the powder also playing vital role, coarser powder with 35 mesh will give better results. Cryogenic pulverising is again costly affair for PP, ABS, Nylon, EVA. Globally micro-palletising is picking up for better powder size distribution.
Marking and labelling:
Primary challenge on PE products is printing. By the surface adhesion advancements, Corona or Flame treatment may be only option for printing. Post-moulding labelling followed by heat treatment is an option available. In recent times In-mould labelling is becoming popular and providing permanent marking.
Use of Recycled materials:
Usage of recycled materials would be a welcome step, though caution here is using appropriate quality and input must. Unknown sourced recycle materials would be hazardous to industry as well as actual users. Associations, customer forums, seminar / conferences are playing vital use for quality water tanks and use of recycled materials.
Need of the hour: Reprocess materials are major threat for quality of the tanks, Health and Hygiene factor. Standardisation must require for all the BIS and non-BIS water tanks. Automation and close –oven better heat control. Rapid production with new large size oven machines. Shifting from manual fabricated moulds to CNC machined moulds.
Non-tank sector Highlight’s:
High entry barrier, advancements require for machine, moulds and operations. Higher investments than tank sector is the barrier to restrict un-organised small players. Better control and higher level of automation for higher quality of products. Be creative, be passionate, invest in designs / moulds, risk-taking are the key attributes requires to work in non-tank sector. Better margins, Less competition, higher value –addition. Non-tank applications hold market share of 30% in Indian Rotomolding market. This sector is growing very rapidly @ 20% per annum. Major non-tank application sectors are Material handling, Automotive, Clean India Mission, Road safety, Furniture’s, Toy’s, Retail products and Custom Moulding. Few rotomolders are predominantly in to business of non-tank applications and few customers are in both tanks and non-tanks businesses. Mannequins and Retail products are highest margin products in India.
Infrastructure projects like generating high demand of roto products like Smart cities, State // National Highways/ Expressways and Railways/Metro/Bullet trains. New growth generated by Assam, Telangana, Andhra Pradesh, Orrisa, North east, Chhattisgarh states . Clean-India-mission, Namami-Gange (Ganga River cleaning), Kumbh Melas, etc generating huge demands. High emission norms set by Government-Of-India generating new business opportunities in commercial Automotive sector. BHARAT emission norms for commercial vehicles generating new potentials for Diesel Fuel tanks, Canopy, Urea tanks (AdBlue tanks) Roto Mitra Forum playing a vital role in growth of rotomoulding industry in India. We have a platform for technical, business development, product development for challenging products.
Manoj Patria
7738383558
manoj.k.patria28@gmail.com